An engineering company has been fined after an apprentice was injured by a lathe.
Health & Safety Executive investigators found the company had failed to carry out correct control measures and implement a safe system of work.
Exposed Moving Parts
The court heard “safeguarding” interlocks in a CNC lathe were overridden to allow operation while doors were open – the apprentice was subsequently injured when his clothing became entangled in the lathe’s rotating stock bar.
Hyspec Engineering Limited pleaded guilty to breaking the Provision & Use of Work Equipment Regulations 1998 and was fined £80,000.
The HSE said: “This incident could so easily have been avoided by simply carrying out correct control measures and safe working practices. Whilst the employee suffered serious injuries, the consequences could have been so much worse”.
It added “Companies should be aware that HSE will not hesitate to take appropriate enforcement action against those that fall below the required standard”.
In order to prevent enforcement action, it is always advisable to seek support from health and safety experts.
Safe Working Tips
The HSE recommend the following control measures:
Before Starting
Before using machinery, think about what risks may occur and how they can be managed:
- Check the machine is complete – are all safeguards fitted and free from defects? The term ‘safeguards’ includes guards, interlocks, two-hand controls, light guards, pressure-sensitive mats, etc. By law, the supplier must provide the right safeguards and inform buyers of any ‘residual’ risks that could not be designed out.
- Produce a safe system of work for using and maintaining the machine. Maintenance may require inspection of critical features where deterioration could cause risk. Also look at the residual risks identified by the manufacturer in the information/instructions provided with the machine – make sure they are included in the safe system of work.
- Make sure every static machine has been installed properly and is stable – usually fixed down.
- Choose the right machine for the job and do not put machines where customers or visitors may be exposed to risk.
- Check new machines are CE marked and supplied with a Declaration of Conformity.
Effective Inductions
There are a number of simple steps you can take to ensure inductions are effective, and to protect both your employees and your business.
Machinery Standards
Make sure that machinery is:
- Safe for any work that has to be done – when setting up, during normal use, when clearing blockages, when carrying out repairs for breakdowns, and during planned maintenance; and
- Properly switched off, isolated or locked-off before taking any action to remove blockages, clean or adjust.
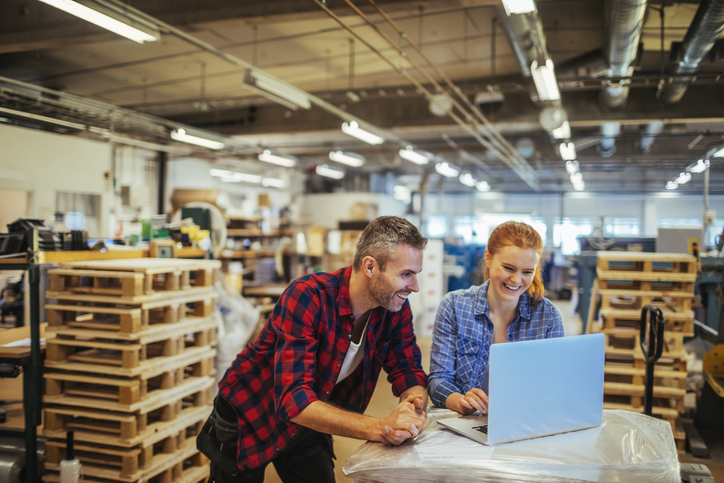
Identify and deal with risks from badly-designed safeguards. Safeguards may be inconvenient to use or easily overridden, encouraging workers as in the above case to risk injury and break the law. If your workers are overriding safeguards, find out why and take appropriate action to deal with their reasons.
Preventing Access to Dangerous Parts
Measures to prevent access to dangerous parts should be taken in the following order – it may be necessary to use a combination of measures:
- Whenever practical, use fixed guards (e.g. guards that are secured with screws or nuts and bolts) to enclose the dangerous parts. Use the best material for these guards – plastic may be easy to see through but may easily be damaged. Where using wire mesh or similar materials, make sure the holes are not large enough to allow access to moving parts.
- If fixed guards are not practical, use other methods, e.g. interlock the guard so that the machine cannot start before the guard is closed and cannot be opened while the machine is still moving. In some cases, trip systems, such as photoelectric devices, pressure-sensitive mats or automatic guards may be used if other guards are not practical.
- Where guards cannot give full protection, use jigs, holders, push sticks, etc., – if practical.
- Control any remaining risk by providing the operator with the necessary information, instruction, training, supervision and appropriate safety equipment.
Need Help?
If you want to make sure your induction training is adequate, speak with one of our experienced consultants for practical advice and guidance.