BLOG
Health and safety in logistics | 5 areas of focus for 2021
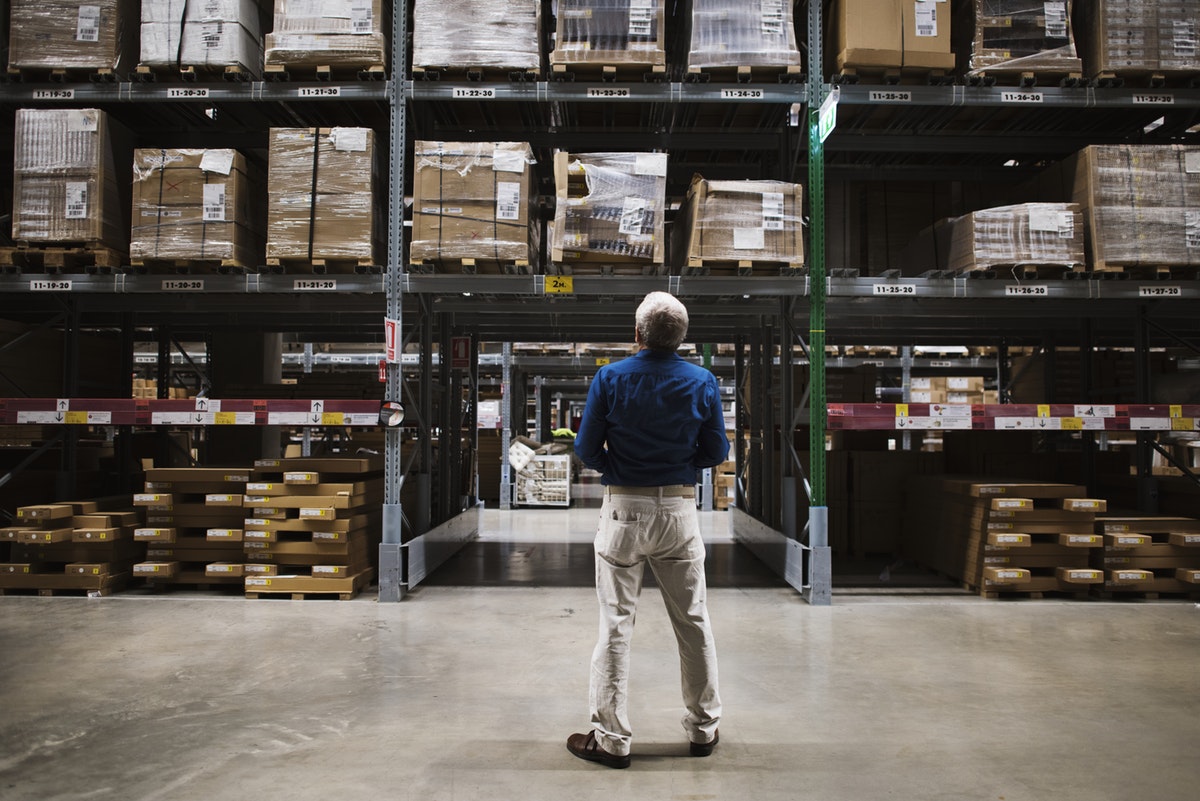
The logistics industry vitally ensures the storage and delivery of goods around the country. It involves not only haulage and distribution but warehousing as well. However, the hazardous nature of its operations means that the industry has a high accident rate. This is partly due to the size and weight of some of the loads involved and the vehicles and equipment required to transport them.
In 2019/20, the Health and Safety Executive (HSE) reported the following transportation and storage sector incident figures:
- 52,000 workers suffering from work-related ill health: musculoskeletal disorders (43%), stress, depression or anxiety (31%) and other illness (26%).
- 11 fatal injuries to workers – broadly similar to the five-year average of 14 fatalities per year – of which 35% were due to being struck by a moving vehicle, 22% resulted from a fall from height, and 13% involved being struck by a moving/falling object.
- 28,000 non-fatal injuries: slip, trip or fall (32%), lifting/carrying (24%) and being struck by a moving/falling object (11%).
The national lockdowns have seen online retail shopping and delivery boom, which has boosted logistics and warehouse operations. However, with heightened demand comes heightened responsibility – employers have both a legal and moral duty to ensure the health and safety of their employees and others.
Hauliers, warehouses and storage facilities are under immense pressure to meet increased consumer demand while at the same time maintaining a safe working environment. Indeed, the HSE’s “spot check” inspection campaign is currently focused on logistics and transport businesses, checking whether goods are being safely stored and despatched.
With the HSE on the warpath, consider reviewing the following areas:
Your safety management system
Given the potential for spot checks, now is the time to make sure you have a robust safety management system and can demonstrate compliance.
Do your current arrangements comply with your legal obligations? Have you reviewed your policies and risk assessments recently? It’s essential that thorough, pro-active risk assessments are undertaken and regularly reviewed. Make sure all relevant risks are covered and that a suitable person is assigned to each issue.
HSE inspectors will want to know how you allocate certain tasks and jobs to individuals and oversee that they are being met. Do people understand their responsibilities? Do you have visibility over the safety performance of different sites? Are vehicle checks and other statutory checks up to date? In essence, can you demonstrate compliance with the regulatory requirements and guidance if inspected?
Demonstrating compliance will improve the defensibility of any claim. Last year, Amazon found itself accused of “failing to provide a safe working environment” after a series of serious incidents were reported to have taken place at its UK storage facilities.
One way to guarantee compliance is by conducting a health and safety audit. While an audit can be produced internally or externally, the auditor should be independent of the part of the organisation being audited. Whichever approach is taken, it must be led by a “competent person”.
How we can help
If you’re not fully confident that you have everything covered, our Health & Safety specialists can take a systematic look at your workplace and current arrangements, identify any areas where you fall short, and get you to where you need to be.
And, if you’re looking for a simple way to stay on top of compliance on a daily basis, our market-leading software, MyH&S, allows you to see the risk status of multiple sites in real time, lets you assign responsibility for tasks, and provides paperless evidence of compliance.
Training
Employers have a legal responsibility to provide staff with the necessary information, instruction, training and supervision relating to their role. When was the last time you revisited staff training needs? Is it time for a refresher? Has the increased consumer demand seen you take on more workers, and have they all had the requisite training to do their role safely?
It’s vital that all new staff receive training and existing staff are kept up to date with evolving safety culture and procedures. Increased warehouse health and safety knowledge will bring about greater observance of best safety practices.
One unprecedented challenge right now is COVID-19. Can your workplace operate within the social distancing two-metre plus rule? If not, it may be reduced to one, but you are obligated to provide training on the new procedures to operate within one metre.
How we can help
If you struggle to find time for training, our remote e-Learning courses are a convenient solution. With e-Learning, workers can complete courses in their own time, at their own pace, allowing you to continue to meet your responsibilities with minimal disruption during this hectic period.
Courses include Accident Reporting (RIDDOR), Manual Handling, Safe Movement of Vehicles, Lift Truck Safety, COVID Response and more.
Visiting client sites
The Health & Safety at Work etc Act 1974 says every employer must take “reasonably practicable” steps to protect the health, safety and welfare “at work” of all their employees. “At work” doesn’t just mean in the workplace – the required protective steps extend to occasions when your employees visit other locations and client sites.
The duty to protect workers both on and off site is more important than ever due to COVID-19. Have you got the right procedures in place and are they working as intended? For example, do your workers perform proper safety checks before and during client visits? If not, you will be falling short of requirements.
Do you need support?
Speak to us for an honest, no obligation chat on:
0345 226 8393 Lines are open 9am – 5pm
Lone working
Similarly, are you protecting lone workers from health and safety risks? Supply chains have been strained by the changing economic lockdown circumstances and the surge in online retail business has increased the numbers employed in logistics and supply chain roles. However, many SME logistics firms will likely have employees, in a variety of roles, working frequently alone or remotely.
What’s more, often awkward shift patterns necessitate workers operating out-of-sight of, or at different times, from colleagues.
Have the risks associated with working unsupervised been carefully assessed? Have you implemented sensible precautions to reduce those risks? We discuss the steps you can take to manage lone working risks here.
How we can help
We can offer practical advice on precautionary measures, ensure you have an effective lone working policy in place, and provide e-Learning training for employees and managers to raise awareness of risks, controls and responsibilities.
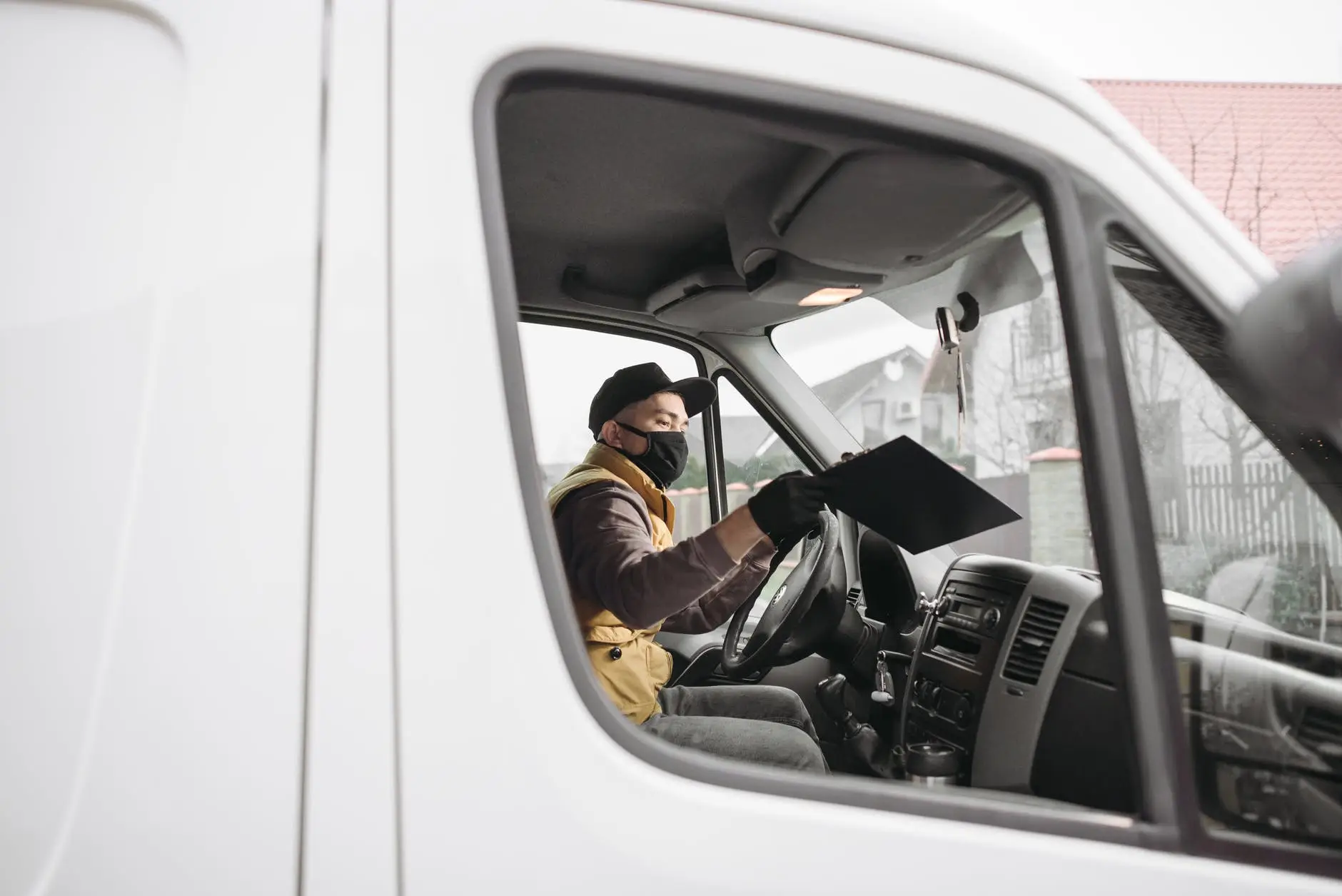
‘Basic’ everyday risks
Slips trips and falls, manual handling, load security and safe vehicle movement are part and parcel of good health and safety management in logistics. While COVID-19 remains a clear focus, it’s important that COVID risk management doesn’t detract from all other ever-present and inherent risks present in your environment.
By its very nature, the logistics industry exposes workers to a wide variety of risks: not only accidents on the road and deaths and injuries resulting from unsafe forklift use but also the consequences of poor fire safety, long-term health risks due to poor manual handling techniques, and problems relating to mental health. Thousands of such incidents occur every year.
As an employer, you are legally required to protect the overall health, safety and wellbeing of employees and others, and COVID-19 hasn’t removed other statutory health and safety obligations that normally fall upon you. This means continuing to identify all hazards within your workplace and taking steps to control the risks arising from those hazards.
For example, forklifts are essential to logistics operation but pose a significant threat to workplace safety, accounting for 25% of UK workplace transport injuries. Where staff and machinery operate in close proximity, maintaining situational awareness is critical. Cost permitting, minimise the risk of collision through proximity warning and alert systems, 360° cameras, active RFID tags and other interactive equipment.
Make sure you are managing these basic risks and read our 8 warehouse safety tips.
Need a helping hand?
Time pressures, lack of resources and the temptation to cut corners, especially during busy operating periods, often leads to neglect of proper safety practices. However, breaches can mean a fine of up to £20,000, and for serious breaches that endanger life, fines are unlimited. In the transport and logistics sector, fines have reached £4 million, and in the most serious of cases, employers also face imprisonment. Of course, there’s also the added risk of civil claims and the reputational damage to your business.
Support from Ellis Whittam can help to dramatically reduce risk to your business and your people, give you the confidence in your compliance, and ultimately enhance productivity and efficiency by promoting a positive safety culture. If you would benefit from access to a named Health & Safety specialist, who will work with you to raise standards and keep you on the right track, call 0345 226 8393 or request your free consultation using the button below.
Sign up for the latest news & insights
Resources
Latest News & Insights
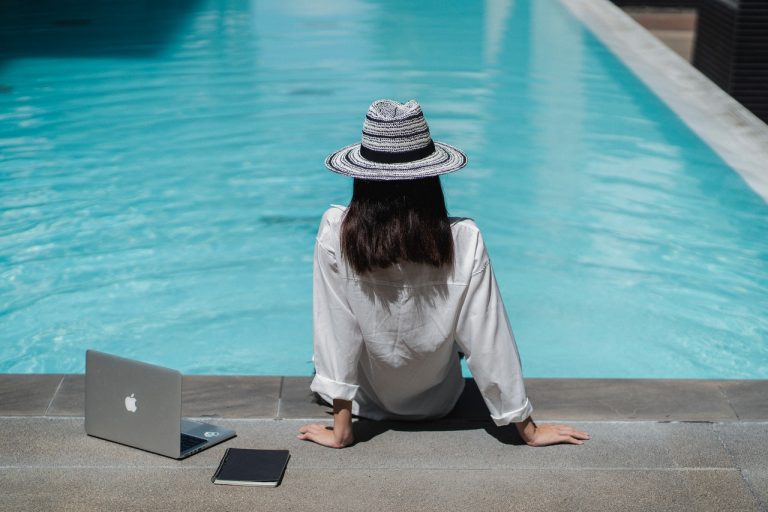
Work from wherever? | Things to consider before allowing employees to work from abroad
BLOG Written by Alexandra Farmer on 25 May 2022 A few years ago, the idea of working from anywhere in the world seemed like a pipe dream.
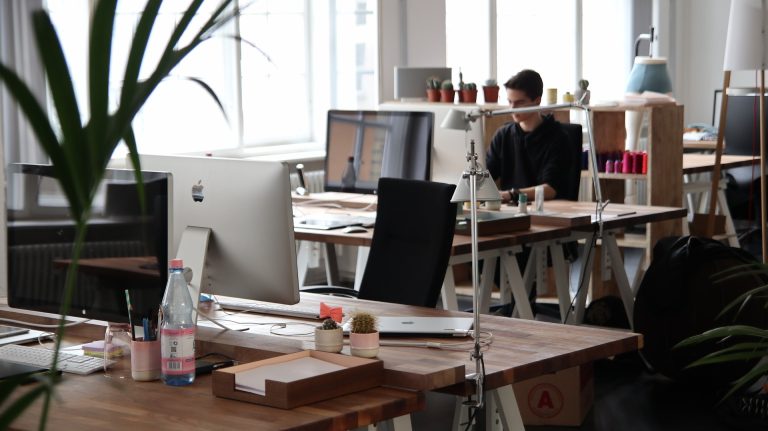
Reduced workforce? Here’s 5 health and safety areas you need to revisit
BLOG Written by Charles Spencer on 18 May 2022 In 2022, a growing number of businesses have moved, or are in the process of moving,
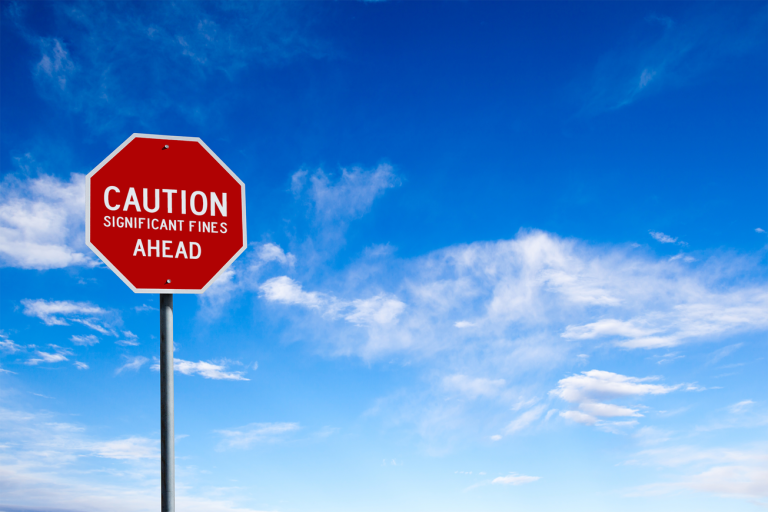
Fee for Intervention | Why health and safety breaches could cost your business more in 2022
BLOG Written on 16 May 2022 It’s a well-known fact that poor health and safety practices cost businesses money. And with the HSE recently announcing yet another
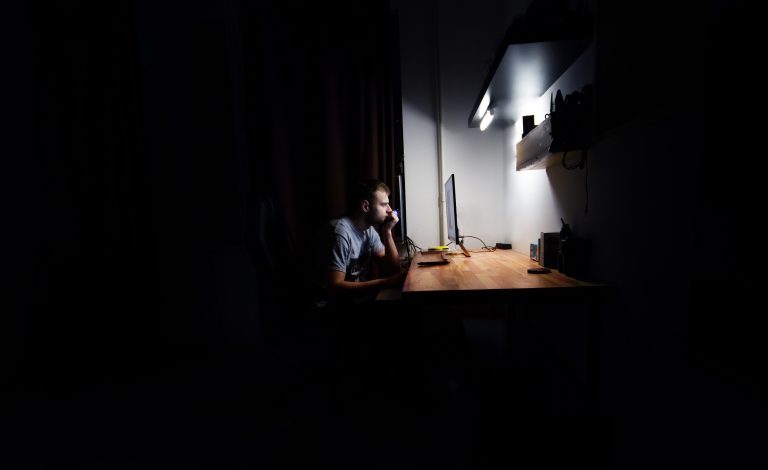
Remote work isolation | How employers can help combat loneliness
BLOG Written on 12 February 2021 While the benefits of remote work are seemingly boundless, often overlooked is the isolation and disconnectedness that it can
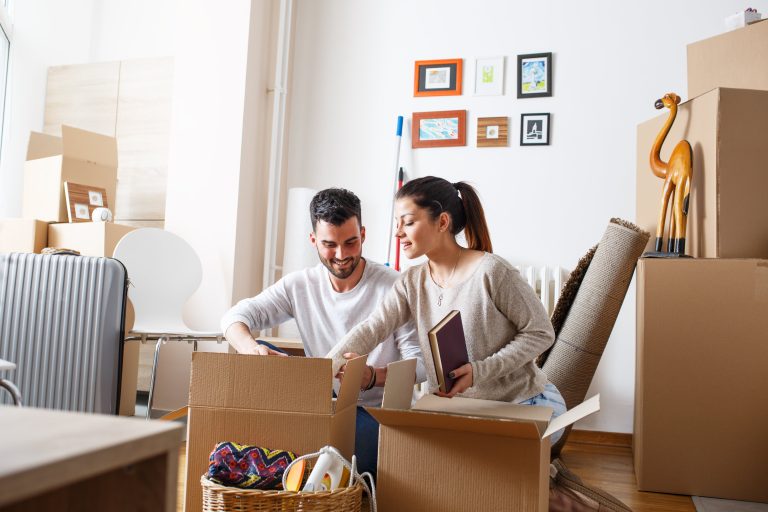
Time off for getting married or moving house
BLOG Written on 12 May 2022 There are certain big life events that can sometimes get in the way of work. Whether it’s a wedding
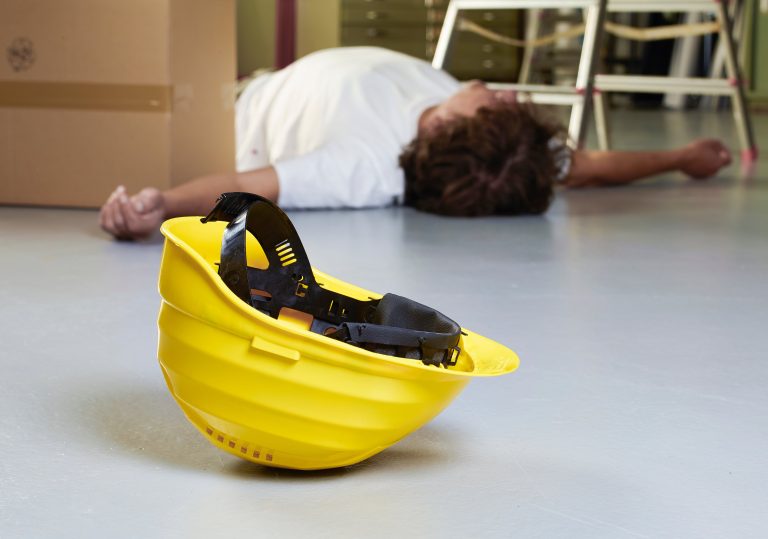
Recent cases highlight continued work at height failings
BLOG Written on 6 May 2022 Working at height continues to be the leading cause of work-related fatality. According to most recent HSE figures, these
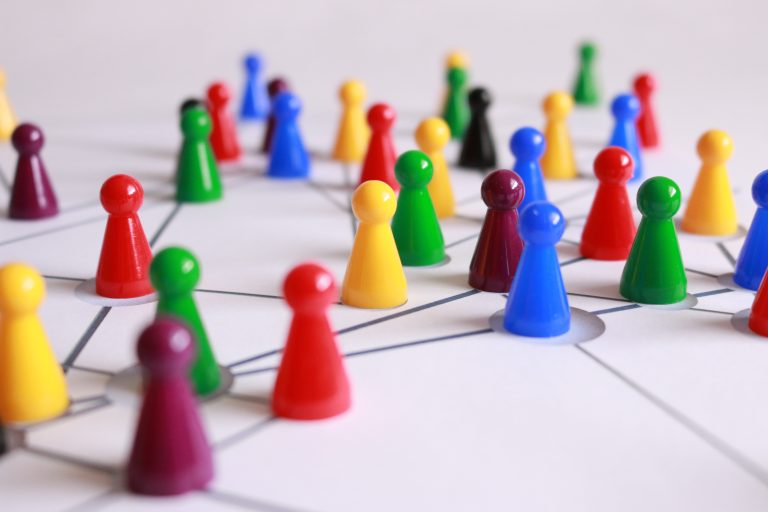
Managing organisational change | How to keep people happy
BLOG Written on 28 February 2022 In the direst of circumstances, humanity’s true capacity for adaptation and perseverance can be realised. Where the business world
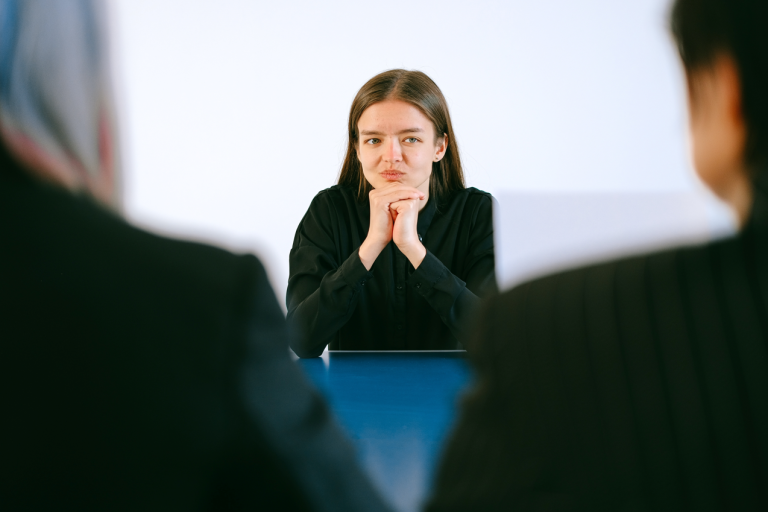
5 ways to combat 2022’s recruitment challenges when you can’t pay more
BLOG Written by Christian Vincent and Hannah Copeland on 15 April 2022 In 2022, recruitment and retention are fast becoming employers’ biggest challenges. With people
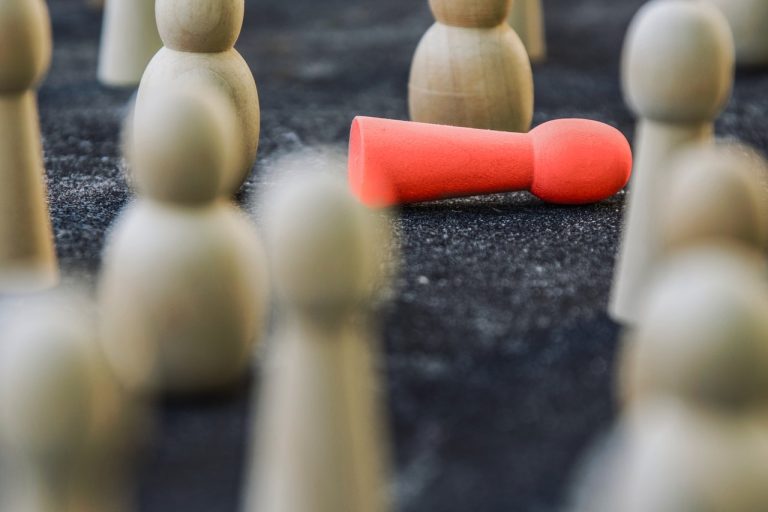
A war of words | Managing employees’ political views on the Russia-Ukraine conflict
BLOG Written by Lesley Rennie on 13 April 2022 The war in Ukraine, and the daily news reports of fatalities, continues to spark conversation in