Despite being dangerous places to work, warehouse businesses sometimes fail to manage risk properly. This is because they take a 'general' approach to warehouse safety.
In reality, warehousing work creates numerous specific and unique health and safety hazards that need to be identified and properly managed in order to prevent harm.
Following reports that more than 600 Amazon workers have been seriously injured or narrowly avoided an accident in the last three years, we discuss eight components of good warehouse safety, including some common hazards and practical prevention tips.
1. Forklifts
Forklifts are vital to the efficient operation of warehouses and storage facilities. However, incorrect forklift use is the most frequently cited warehouse hazard – endangering operators, nearby workers and property.
Reversing
Particular care should be taken when reversing, as almost a quarter of all deaths involving vehicles at work occur when drivers reverse. Reversing should be avoided wherever possible – and if it can’t be avoided, make sure drivers have someone to spot them or other visibility support.
By using a one-way system and planning routes, you can minimise the need for drivers to reverse and maximise visibility. Setting up mirrors will also aid driver vision when manoeuvring around corners or reversing. And of course, make sure workers look both ways when leaving aisles.
Stick to the following warehouse health and safety rules for forklifts:
- Operators should be competent and have undergone practical training.
- No one under 18 should operate a forklift.
- Drivers should not exceed 5mph. Put up signs to remind them.
6 practical tips for reducing forklift/vehicle risk:
Provide refresher training for operatives. Reinforce the importance of attentiveness, vehicles being able to support loads and driving slowly.
Regularly evaluate activities. Observe operators to check that vehicles are being used safely and in accordance with the training given.
Performing daily pre-start inspections. Provide drivers with a daily check list, for example, dashboard warning lights, deflated tyres, faulty seat belts, strange noises, etc.
Have vehicles regularly inspected and maintained by trained professionals.
Ensure warning signs and mechanisms are in place to keep pedestrians and vehicles apart, especially around blind corners.
Maintain floors to prevent overturning or damage to vehicles. Make sure floors aren’t too steep, uneven or damaged.
2. Housekeeping
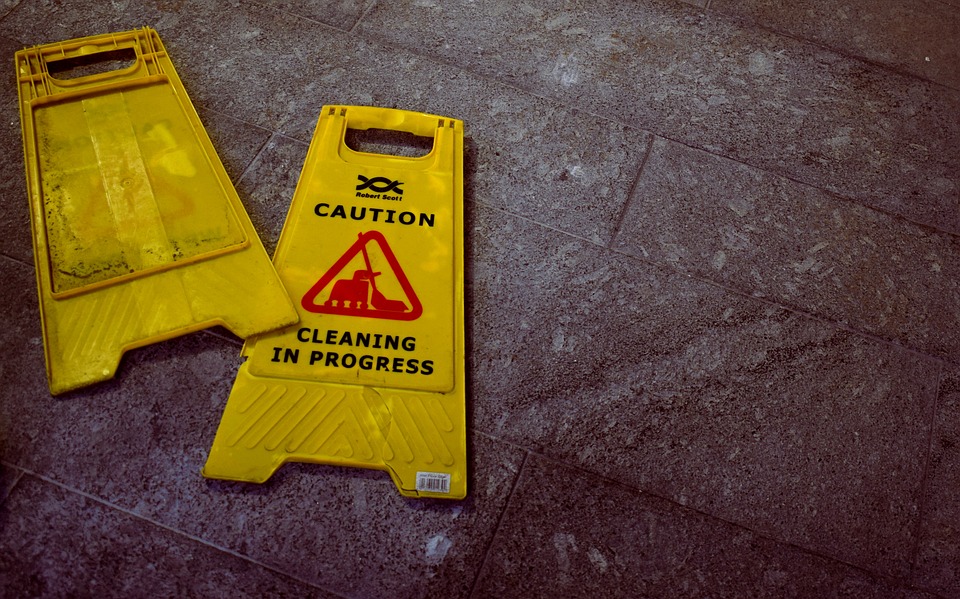
Large and busy warehouses typically see inventory items being moved in and out all day long, quickly leading to a messy environment. Aisles and passageways that aren’t kept clear and in good condition can cause workers to slip, trip or fall.
Slips, trips and falls are the number one cause of non-fatal injuries in UK workplaces. Fortunately, these injuries are fairly simple and inexpensive to prevent.
Safeguard your environment by:
- Having measures in place to quickly remove unwanted items. Make sure staff know to follow good housekeeping practices by quickly removing obstructions from paths, keeping cables tidied away, cleaning up spillages, etc.
- Ensuring cleaning staff display appropriate warning signs. Try to schedule cleaning outside of normal working hours so that fewer people are put at risk. Also make sure that cleaners use the correct method and detergent for the type of warehouse floor.
- Using anti-slip paint. This will reduce the slip quality of floor surfaces, prevent dust from building up, minimise wear and tear, and improve cleaning.
- Ensuring stairs have non-slip material and sturdy guardrails. Anti-slip tape is useful for stairs and other areas where you can’t use anti-slip paint.
- Using non-slip footwear.
- Making sure floors are level. Uneven flooring can cause people to lose their footing, especially if carrying a load.
Important: Lighting should be bright and positioned throughout the warehouse. Warehouse safety signs should be clear – illuminated if possible – and easy to understand.
3. Storage
Improper storage of materials poses a serious risk to workers. Unfortunately, warehouses often have items stacked high, making falling objects a constant hazard.
To reduce risk:
- Heavier loads should only be stacked on lower or middle shelves.
- Loads should be evenly placed and properly positioned.
- Stack items as neatly as possible so that loads don’t shift.
Remind workers to always remove one load at a time and to never over-reach when placing or retrieving items. Staff should be trained to work at height safely. Ladder safety is essential, as misusing or using an unstable ladder can lead to serious injury or even death.
Make sure that:
- Ladders are not used for longer than 30 minutes.
- Users stay off the top three rungs.
- Users maintain three points of contact at all times, for example, two feet and one hand.
4. Conveyors
Conveyor equipment is also commonly used to move goods in warehouses. Conveyors pose serious dangers to workers, particularly when getting caught in moving machinery parts.
Keep workers and others safe by ensuring:
- Conveyors are appropriately safeguarded to protect against the risk of clothing, hair or body parts becoming entangled.
- Proper lock-out procedures are followed during conveyor maintenance and repair.
5. Manual handling
Improper manual handling is the most common cause of injury in warehouses. Workers who repetitively handle or lift materials risk developing musculoskeletal disorders (MSDs), especially if using awkward postures or over-exerting.
Employers can reduce the risk of workers developing MSDs by providing manual handling training, ensuring proper ergonomic postures are adopted (by observing workers carrying or moving loads) and keeping handling tasks to a minimum.
Consider whether loads really need handling:
Can the manual element be reduced through good engineering design/ergonomic workstations?
Could loads be handled in a different way? For example, can a process be carried out without lifting?
Can mechanical aids be used to remove or reduce the manual element?
Remember: If not performed safely, machinery-assisted lifting activities also pose a significant risk. Make sure that operators of lifting equipment know the maximum safe working load.
5. Pallets and racking
Most warehouse workers are required to load and unload pallets on racking. These tasks must be carried out safely so as not to drop pallets, affect the stability of racking or damage other equipment.
To ensure safety:
- Train staff to load pallets securely. Use shrink or stretch wrapping to support pallets and follow a suitable stacking pattern.
- Make sure staff follow the manufacturer’s recommended safe stacking height and weight capacity. Pallets should be evenly stacked, with heaviest on the bottom.
- Instruct staff to inspect pallets before use. Pallets should not have loose nails, splinters, cracks or other issues.
- Instruct workers never to climb on, lean on, or walk over pallets or racking.
- Ensure staff never use pallets or forklifts to access heights.
6. Fire
Warehouses typically have a lot of open space and kindling, meaning a fire would spread extremely quickly.
Good fire safety measures include:
- Carrying out fire drills at least once a year.
- Testing fire alarms weekly, as well as regularly checking other equipment, such as smoke alarms, extinguishers and emergency lighting.
- Creating a fire evacuation and emergency plan and reviewing it regularly to keep it up to date.
- Appointing fire wardens.
7. Training
The procedures or systems you have in place to ensure good warehouse safety are only as good as those implementing them. To ensure health and safety remains a top priority, it’s essential that every employee receives frequent training, followed by enforcement and review. Without this, the measures you put will merely play lip service to health and safety.
Employers often mistakenly think of health and safety training as a one-off event, when it should instead be a recurring practice. All employees, no matter how experienced, must have their training renewed in order to keep them abreast of any changes. New workers should of course be given thorough health and safety induction training before starting even their first task. Training should then be reinforced to ensure the practices and behaviours taught become part of the work culture.
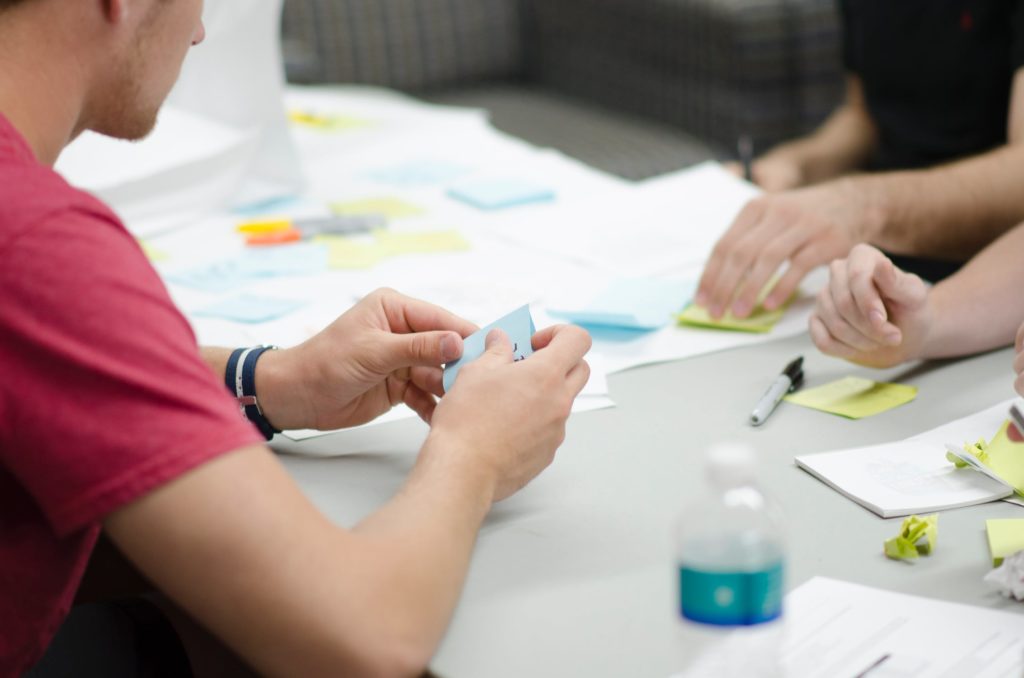
Don’t forget: Provide staff with suitable personal protective equipment (PPE) to prevent exposure to numerous hazards. You’ll need to assess the risks in your warehouse to determine the type of PPE needed. Hard hats and high-vis jackets are essential on most warehouse sites.
Before starting a job, new workers must be advised of all the workplace health and safety risks. A warehouse induction checklist is a good way of making sure they have been informed about those risks. It’s also a good way to check whether a worker has the skills, training and qualifications needed for their role. This is particularly important in high-stress warehouse environments where workers face numerous hazards.
Warehouse induction checklists are an essential safety management tool. They are particularly useful in dealing with typical warehousing problems such as increased exposure to repetitive motions, helping to prevent bodily strain-related injuries.
Warehouse Induction Checklist
Is the new starter familiar with the warehouse Health & Safety Policy and rules?
Does the employee understand the main warehouse safety risks and how they are reduced?
Has the employee been inducted on safe ways to work in a warehouse?
Has the employee received general ergonomics and task-specific warehouse training?
Has the employee been given proper training for the tools and machinery they will be using?
Has the employee received manual handling training and do they know what kind of facility aids/devices are available to help with manual lifting?
Is all of the employee’s training and certification up to date?
Has the employee been provided with suitable personal protective equipment and do they know where additional PPE can be found?
Has the employee been properly trained and outfitted for weather/temperature extremes such as heat stress, cold weather, refrigerated storage areas, etc.?
Does the employee know how to report in and out of the warehouse? Are they familiar with the evacuation procedure? Do they know the location of emergency exits and their fire assembly point?
8. Audits
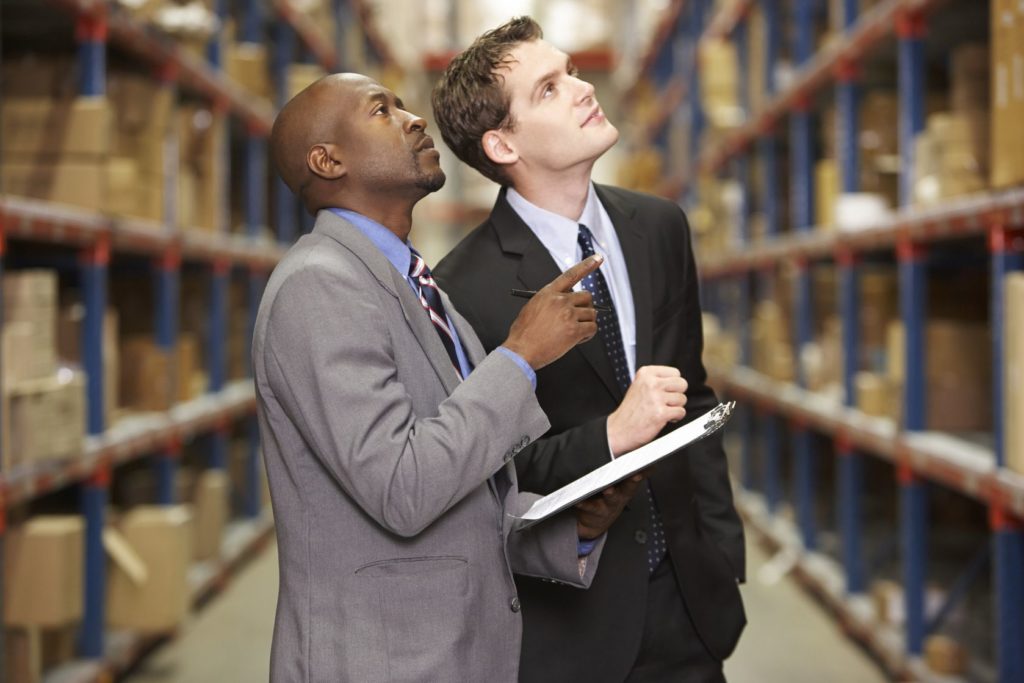
Putting warehouse safety measures in place is one thing but maintaining them long-term is another.
To ensure standards are upheld, it’s good practice to carry out frequent health and safety audits covering all buildings and machinery. Employees should also be audited to check whether their knowledge and behaviours conform with safety procedures.
The goal is to proactively identify any unsafe conditions, such as:
- Workers not wearing PPE.
- Equipment not working properly.
- Cluttered aisles and passageways.
- Obscured safety signs.
- Locked or poorly lit emergency exits.
- Stray cords laid across floors.
- Naked wiring.
- Uneven or damaged flooring or tiling.
Above all, be proactive. Never wait for something to go wrong before taking action.
Useful resources: More advice on keeping your warehouse safe can be found in the HSE’s guide to warehousing and storage.
Offload your health and safety pressures with outsourced support
When you run a fast-paced business, finding the time to manage all aspects of health and safety in line with the law can be difficult. What’s more, if you’re not a health and safety expert, it’s all too easy to miss the mark, resulting in costly absences, enforcement action and fines.
At Ellis Whittam, we help employers in the warehousing, storage and distribution sector reduce risk on a daily basis through unlimited, fixed-fee Health & Safety support. Acting as one of your competent persons, your dedicated consultant will implement a health and safety management system that works for you and help to identify sensible, proportionate solutions to the specific challenges you face.